Introduction
The rise of lithium-ion (li-ion) batteries has revolutionised the way we power our devices, from smartphones to electric vehicles. However, with this innovation comes a significant challenge: the proper disposal and recycling of these batteries. In Australia, the recycling rate for Li-ion batteries is significantly lower compared to other battery types, posing both environmental and logistical problems due to the growing volume of Li-ion battery waste.
Rhino Instruments, dedicated to sustainable and repairable design, embarked on a pioneering project supported by a $46,200 grant from Sustainability Victoria. The project, titled “New Life for Resource Recovery Centre Harvested Lithium Ion Batteries” aims to advance research into reuse, before recycling, of the significant volume of discarded li-ion cells that are still in a serviceable condition.
This case study explores the commercial potential for reuse of discarded Li-ion batteries in Australia, focusing on the technical, economic, and regulatory challenges encountered by Rhino Instruments. By developing a prototype battery management system (BMS) that can accommodate second-hand 18650 cells with mixed capacities, Rhino Instruments aims to extend the life of these batteries and contribute to Australia’s transition to a circular economy.
The results of the project included:
- 59.41% of the 202 cells extracted had more than 80% of their original capacity, highlighting the significant potential for reuse
- A specially designed battery management system that has the potential to allow safe reuse while managing the risks
- That there are pathways to commercial reuse under existing battery and product safety regulations
Important: This research is for informational purposes only and is not intended for personal use. Incorrect use or reuse of any battery, including lithium-ion, can cause fire, explosion, or death. Do not attempt to replicate this research or handle these materials at home. If you do choose to work with batteries, you do so at your own risk, and should ensure you throughly understand the inherent dangers and have the required electronics expertise.
Background
Lithium-ion batteries have become the preferred choice for powering a wide range of devices due to their high energy density, long life, and light weight. Despite these advantages, the disposal and recycling of Li-ion batteries present significant challenges.
In Australia, only about 10% of Li-ion batteries are recycled, compared to over 98% for lead-acid batteries, yet they contain valuable materials such as cobalt, lithium, and nickel. This low recycling rate is due to several factors, including the complexity of the recycling process and the lack of infrastructure. According to the CSIRO, lithium-ion battery waste is growing by 20% per year and could exceed 136,000 tonnes by 2036.
There are also the environmental and human health risks. These cells are still making it into landfill despite e-waste landfill disposal bans, evidenced by the increasingly causing garbage truck fires. Scooters and e-bikes, energy storage facilities and, while more rare, even EVs also go up in smoke.
The situation appears to have worsened since our application was written. As we write this article the Waste Management & Resource Recovery Association of Australia has called for the Federal Government to make an immediate priority of getting batteries out of the waste stream.
Specifically, the risk of the exposure to the chemicals contained within lithium-ion cells should be stated here rather than linked to. From a 2016 technical paper from Global Sustainable Energy Solutions linked to in the CSIRO’s research:
The chemical hazard of this substance presents itself when the electrolyte leaks from the battery casing, such as through a puncture of the battery casing.
LiPF6 is a flammable, hygroscopic (absorbs water), and corrosive compound usually in a liquid state. It reacts very easily with mucous tissues and is explosively reactive to water due to the lithium-ion present in the electrolyte. It causes burns to the skin, eyes and gastrointestinal and respiratory tracts. Severe organ damage, possibly leading to death, from contact with the substance is possible.
Under conditions where LiPF6 is at relatively high temperatures, around 70°C or above, it can cause hydrolysis. But unlike lead-acid, this hydrolysis can prove much deadlier.
Hydrofluoric acid is a very dangerous acid, and it will react corrosively with almost anything, even glass. It can damage lung tissues severely if inhaled, and is damaging to the skin and eye tissues. It is known for causing systemic toxicity, respiratory failure, cardiac arrest, and death even with little physical contact with the compound. If a battery with LiPF6 were to be damaged and spill electrolyte, LiPF6 will start to react with water in the environment and create a dangerous fume.
It would be incredibly dangerous to be near the spillage without any personal protective equipment. Due to the severity of the hazards present, batteries using LiPF6 are designed to contain all the internal components and ensure that any chemical reactions are contained inside the battery casing safely. However, care must be taken to avoid crushing, perforation, or careless disassembly of the battery casing.
Our project “New Life for Resource Recovery Centre Harvested Lithium-ion Batteries” aimed to advance research into reuse, before recycling, of the significant volume of discarded Li-ion cells that are still in a serviceable condition.It explored the commercial potential for reuse of discarded Li-ion batteries in Australia, focusing on the technical, economic, and regulatory challenges. By developing a prototype battery management system (BMS) that can accommodate second-hand 18650 cells with mixed capacities, there is the potential to extend the life of these batteries and contribute to Australia’s transition to a circular economy by showing these cells are a valuable resource.
Our Commitment to Sustainability
Rhino Instruments has a strong commitment to sustainability and repairable design. Before selling a single product, we aimed to create a device with minimal environmental impact. This ethos includes using recyclable materials, designing for longevity, and supporting the right to repair movement. The effort to reuse Li-ion batteries align with these principles, aiming to reduce waste and extend the life of valuable resources.
Methodology
The first phase of the project involved the collection, disassembly, and testing of discarded battery packs from a local resource recovery centre.
The second phase was understanding how a lithium-ion cell needs to be charged and discharged, investigating methods of cell isolation and thermal management, and building prototype electronics that implement these principles. Then integrating these ideas into a refined printed circuit board that could be demonstrated and evaluated for performance.
The following steps were undertaken:
Collection and Initial Inspection
Battery packs were sourced from a local resource recovery centre. Packs with visible external damage were excluded from further testing to ensure safety and feasibility.
Disassembly
Disassembling a lithium-ion battery pack is a tricky task. Each manufacturer builds their enclosure differently, with no manuals available. Some have screws holding them together, others hidden clips and glue. The cells inside are electrically connected to each other and live. Some packs have sustained damage that isn’t visible on the outside, these packs were excluded from further testing.
To undertake this process safely, we developed a solid procedure involving a risk assessment, safety protocols, PPE, accessible equipment for minor issues, and an emergency plan for worst-case scenarios.
With this plan in place, we were ready to go. As each pack was disassembled, we took note of the following:
- Assigned Pack ID
- Date Logged
- Manufacturer
- Pack Model Number
- Pack Voltage (New)
- Pack Amp hours (New)
- Number of Cells
- Cell Type/Size
- Physical Condition
- External Case Accessibility/Difficulty
- External Case Tools/Method
- Internal Enclosure Accessibility/Difficulty
- Internal enclosure Tools/Method
- Original Use
- Photo
- Any Notes
Testing and Evaluation
Extracted cells were tested for their initial voltage. Cells with an initial voltage of 2.5 volts or greater were subjected to further capacity testing using a commercial charger. The results were recorded, and cells were graded based on their remaining capacity.
We also took extensive notes on pack disassembly, grading each pack for external and internal ease of disassembly and noting the tools used.
Data Analysis
The cell capacity tests were a crucial part of assessing the viability of reusing discarded Li-ion cells. The tests aimed to determine the remaining capacity of each cell compared to its nominal capacity as specified in the datasheet. This analysis provides insights into the potential for reusing these cells and the effectiveness of the prototype Battery Management System (BMS).
BMS Prototyping
Several electronics prototypes were tested starting with the charge and discharge of a single cell. In this phase we investigated the difference between Constant Current charging and Constant Voltage charging, as well as the different phases cells go through that call for each type of charging.
Once confident with a single cell, a second prototype was created. This allowed the same methods to be applied to two isolated cells that output to a single point where a small load could be attached. Going from a single cell to multiple cells formed the basis for being able to string together any number of cells.
BMS Integration and Testing
The third phase was developing a PCB specifically for managing Li-ion cells. Voltage data was logged during charge and discharge cycle testing to evaluate the performance and safety of the BMS. We also used a thermal camera to look at the cell temperatures under different conditions, and tested the behaviour of the board under conditions where it detected that a cell had reached an unsafe temperature.
Research Results
Our research results are broken up into four categories:
- Viability of discarded cells
- Viability of battery pack disassembly
- Regulatory findings
- Technical findings (Battery Management System design)
Overall the results are highly positive and we consider the project highly successful.
- We found a high percentage of the cells tested were viable (59.4%)
- There is a high amount of labour involved in cell extraction which could affect the viability of cell reuse
- Extraction could be made easier with improved external and internal enclosure designs
- The intricacies of product regulatory compliance are best left to an expert regulatory assessment. Broadly though, there does not appear to be a regulatory limitation on cell reuse in Australia if detailed evaluation of data and reports pertaining to safety-critical components can be performed in accordance with relevant battery safety standards such as IEC 62133-2, and all relevant product standards are met
- Our final BMS prototype is highly integrated and we are satisfied it operates as expected
Results on Viability of Discarded Cells
- We found 59.41% of the 202 cells we extracted still had a capacity of 80% or greater.
- Of the 202 cells, 71.29% (144) were determined testable for a capacity check
- Of the 144 cells, 84.62% still had more than 80% capacity
- Download CSV dataset – discarded-18650-cell-test-log.csv
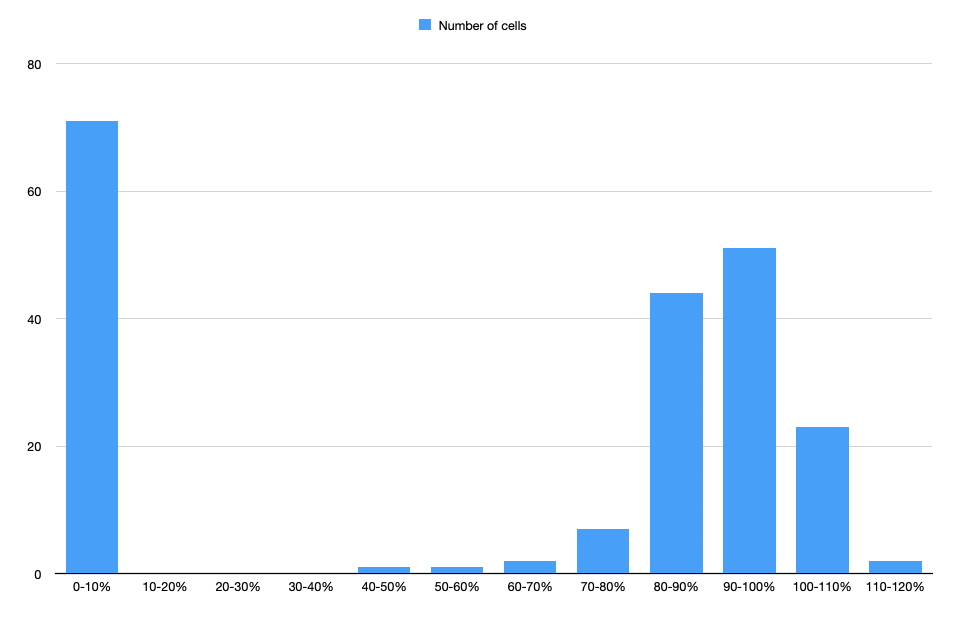
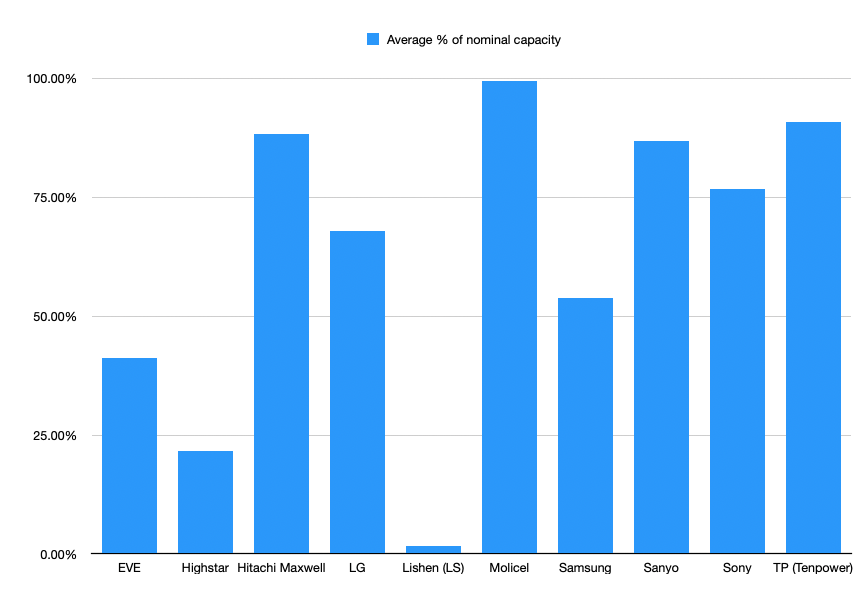
Results on viability of battery pack disassembly
Download CSV dataset – discarded-battery-pack-disassembly-log.csv
The most interesting discovery in this process was rating the accessibility of the external and internal enclosures. Pack accessibility is directly related to the viability of the circular economy. If it’s too hard to dismantle a pack, it becomes unviable to recover the raw materials in their highest value form.
Originally, we had one rating but we quickly realised there are two enclosures: the one visible to the world and the one inside that holds the cells firm.
If we had to pick a favourite brand, it’s Ryobi. Somewhat sleek with some hidden screws but overall they seem to have the balance right. They consistently rated three (average difficulty) out of five for external and internal disassembly.
External case designs
In some cases, the difficulty of accessing the external case appeared to be about the sleekness of the design. The leading example of this is the Dyson cordless vacuum packs. The screwless design and the way the two plastic shells meet almost seamlessly make for a very nice-looking product that fits well in a home environment. Unfortunately, that seamlessness also makes it impossible to open the case quickly and without destroying it.
At the other end of the spectrum, the Dewalt packs were super easy to open with eight simple Torx screws. The design of these battery packs is still pleasing, but they do look like they belong on the worksite and not in a kitchen.
Internal case designs
A high degree of difficulty was encountered once we were inside the packs. The cells need to be solidly held together so they can be electrically connected. Also, if you read the datasheet for any Li-ion cell, you’ll note they are sensitive to impact and vibration. Therefore, product designers need to consider where the packs are likely to be used. Longevity, reliability, pack size, and the safety of the end user must be the balanced.
Dewalt and Milwaukee are two brands commonly seen on construction sites. These packs are likely the most abused on the market. Their packs were mostly rated ‘difficult’ to ‘very difficult’ to dismantle internally, but it seemed somewhat justified. On the other end of the scale, there are Dyson cordless vacuum packs which live in the home and are far less likely to experience regular impact and vibration. However, most of Dyson’s internal pack structures were almost as difficult to dismantle as construction-grade packs. In some examples, they were also more wasteful due to unremovable glue (likely part of thermal monitoring) stuck to several cells, preventing the recovery of those cells. There is an exception with Dyson, however. There appeared to be internal accessibility improvements in newer revisions of their packs, which deserves credit and is covered below.
The typical exterior condition of a Milwaukee or Dewalt battery pack shows they live a harder life and need to be more durable to protect the Li-ion cells during normal use.
A real bright spot in our dismantling journey was the discovery of invisible internal design improvements inside later model Dyson cordless vacuum battery packs.
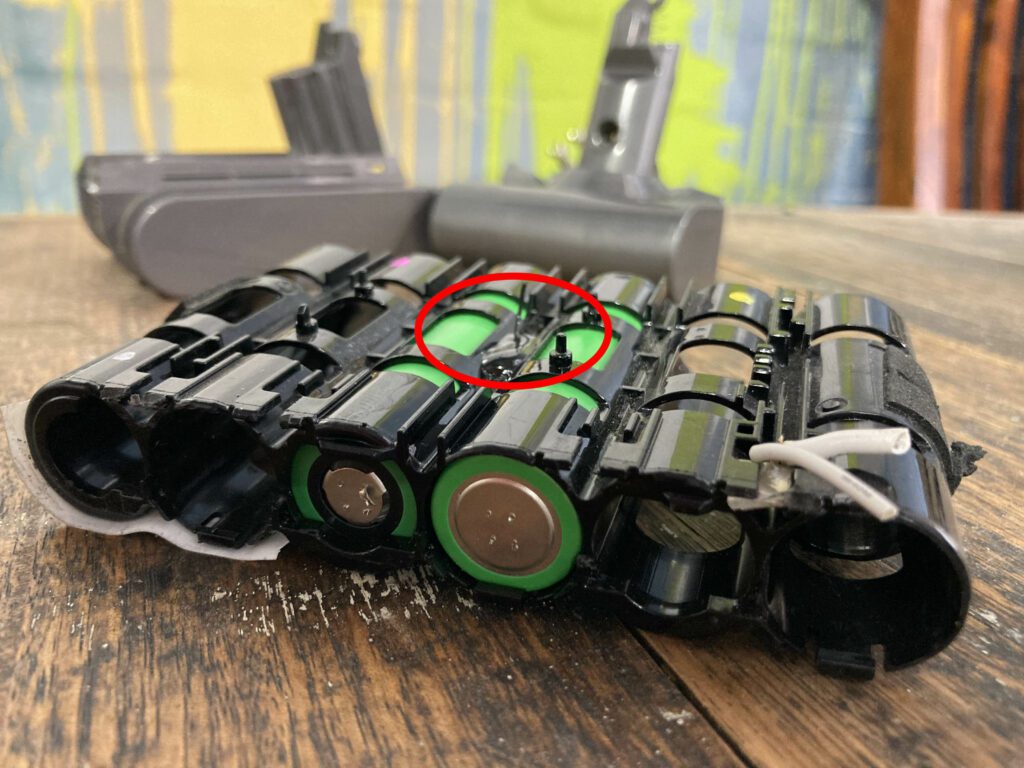
You can see the early packs have used glue inside. Our guess is that this is thermal glue that allows the temperature of two cells to be transferred to a sensor monitoring conditions. Cell temperature is an important metric in determining safe charging and operating conditions. If things get too hot, it’s important to slow charging or shut everything down to avoid fire or explosion. Quality packs that do this well and comply with regulations are the least likely to cause issues. Fires that you often see in the news are most likely non-compliant imported scooters and other products that haven’t passed stringent independent safety testing.
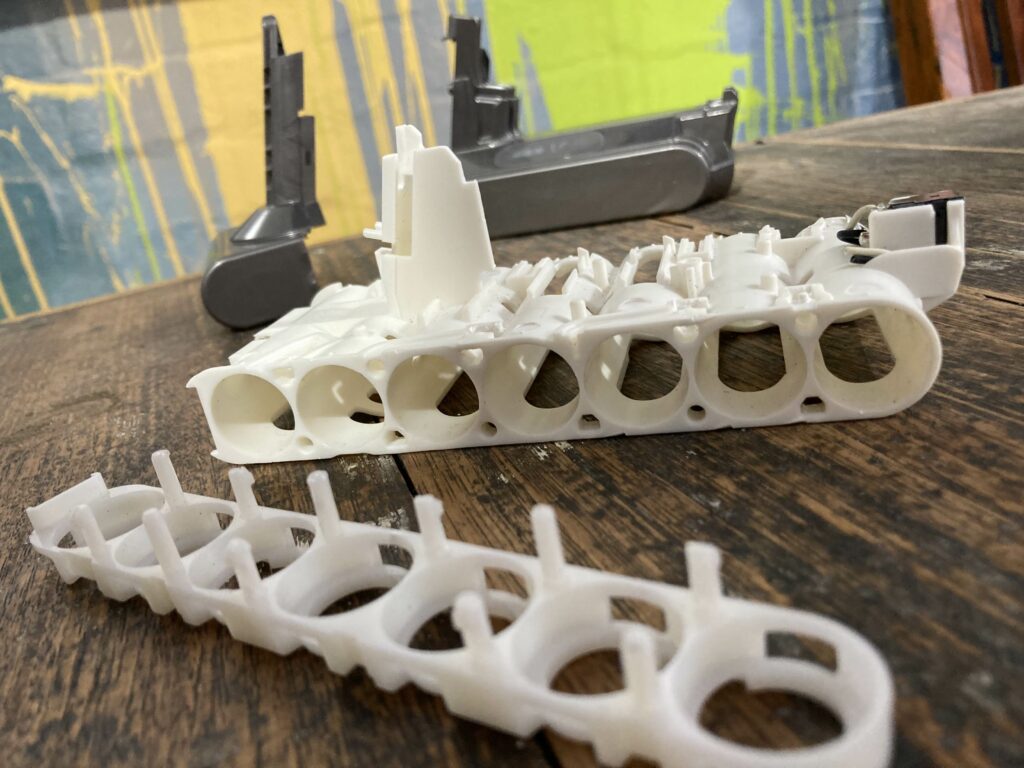
The later packs would have a similar ability to monitor cell conditions; however, these packs come apart with clips, and no cells are glued in, meaning all cells are fully extractable. Dyson appears to have achieved this without compromising the safety or reliability of their pack.
As we say, this was a pleasant surprise – once we were inside the pack. We’d still like to see screws on the outside of their packs to further improve end-of-life accessibility.
Regulatory Findings
The intricacies of product regulatory compliance are best left to an expert regulatory assessment. Broadly though, there does not appear to be a regulatory limitation on cell reuse in Australia if detailed evaluation of data and reports pertaining to safety-critical components can be performed in accordance with relevant battery safety standards such as IEC 62133-2, and all relevant product safety standards are met.
Technical Findings – Battery Management System Prototype
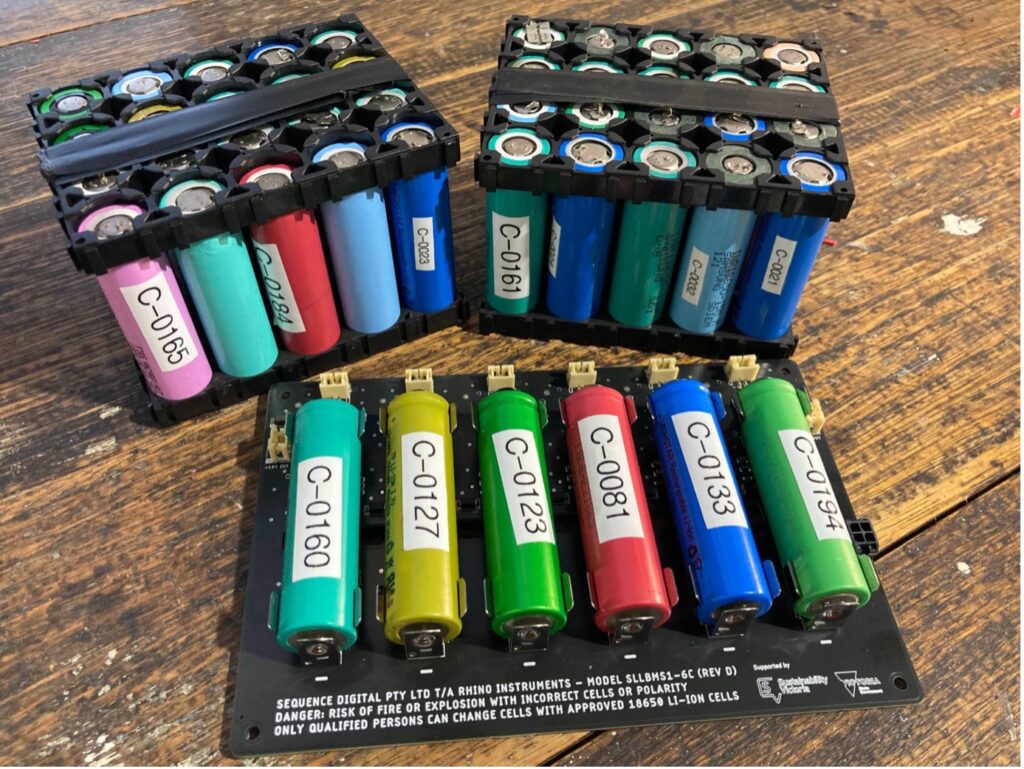
As part of our project we developed our own Battery Management System (BMS) prototype to manage and monitor individual cells. The process began with identifying the key requirements for the BMS, including the ability to handle mixed-capacity cells and ensure safety under varying load conditions. We designed the BMS to isolate cells, prevent overcharging and deep discharge, and monitor temperature to mitigate the risk of thermal runaway.
Prototyping involved iterative testing and refinement. The final prototype is running a modified version of our RM1 device using a batch of six discarded cells. This device is being actively used at the City of Greater Geelong’s $3M Garden Organics Processing Facility for 12 months across 2024-2025 alongside our regular lead-acid powered RM1 devices.
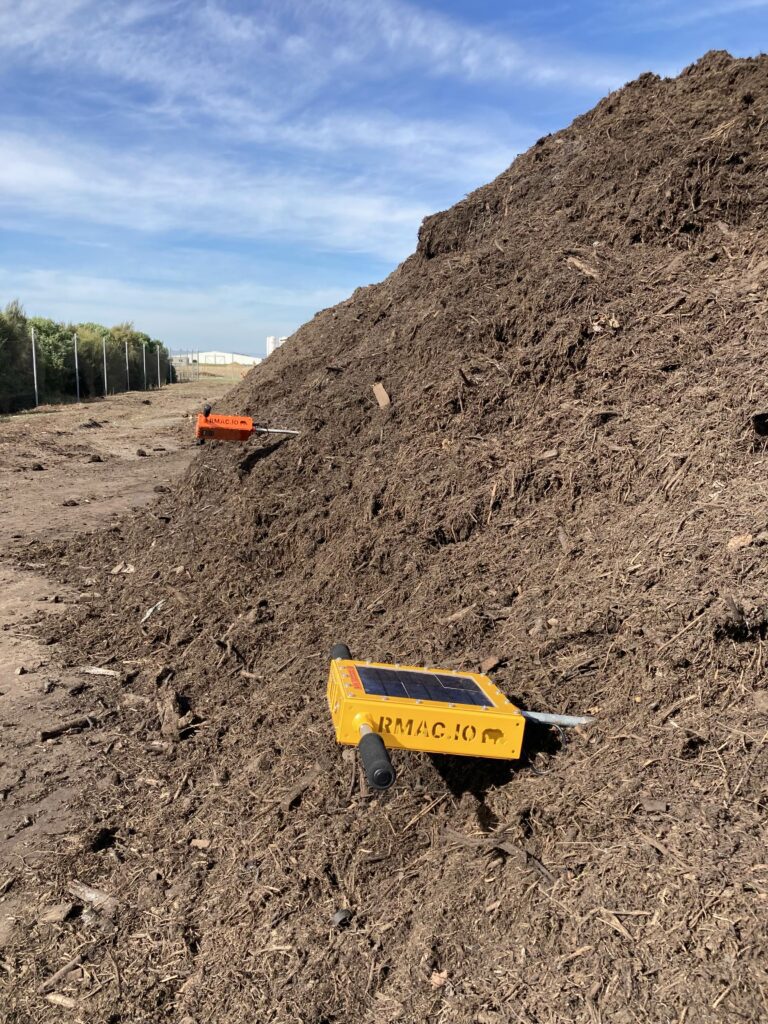
This demonstrates the ability of the BMS to maintain safe operation, thereby validating our design approach for integrating reused Li-ion cells into new devices. The graph below shows cell performance including how C-0167 was showing signs of being weaker than the rest of the pack. Eventually the managing IC determined that it should be treated differently to the rest of the pack and left at lower voltages. This did not appear to affect the overall operation of the pack.
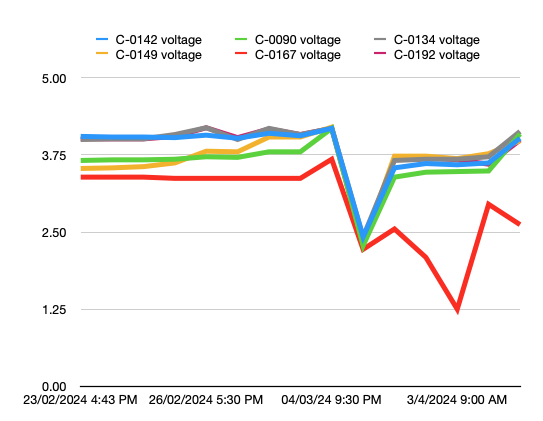
Conclusions
We achieved all aspects of what we set out to do. We showed 18650 Li-ion cell reuse is highly viable from a material availability, regulatory and technical perspective.
Other standard cylindrical cell sizes also show potential where they have been configured in packs electrically connected in series and/or parallel as this increases the likelihood of a mixture of serviceable and spent cells. We have focused on small cordless appliance packs however this applies all the way up to large packs such as inside EVs where there can be thousands of cells.
The main limitations we see to commercial adoption of used lithium-ion cells is:
- Access to a consistent supply of the same cells
- High amount time and labour cost involved in cell extraction
The intricacies of product regulatory compliance are best left to an expert regulatory assessment. Broadly though, compliance requires thorough physical testing of the equipment, along with a detailed evaluation of data and reports pertaining to safety-critical components, such as battery packs and cells, in accordance with relevant battery safety standards such as IEC 62133-2, and satisfying the requirements of any other relevant product safety standards. If a manufacturer passes with a certain cell or set of cells in their product, realistically they need to stick to those specific cells or return to the compliance testing stage again. Discarded cells come in many shapes and sizes with various markings and it can be hard to find consistency.
In addition, just generally it can be quite hard to run a profitable business. There are commercial pressures on manufacturers to keep the product design and manufacturing process as straightforward as possible. Adding circular economy principles into the mix can be challenging.
This commercial reality combined with compliance requirements nudges manufacturers towards traditional and proven ways of doing business.
Changing the Economics of Cell Extraction and Reuse
The transition to an energy system undergirded by battery storage is well underway. The waste is growing. There are serious gaps in the management of discarded batteries and solutions for end-of-life recycling in Australia as highlighted by the CSIRO and evidenced by the flood of recent articles about battery fires. This is in addition to the serious health and safety risks outlined in the background of this document.
If these aspects are taken into consideration, it may change the economics on the viability of extraction and reuse of cells. By subsidising the labour behind collection, disassembly, extraction and testing, a reuse market for consistently available and compliant discarded lithium-ion cells may emerge. That upfront cost could reduce other costs downstream related to the pressure on recycling infrastructure, and fire, health and environmental concerns.
Australian Right to Repair Legislation
With the time and labour cost involved in cell extraction being a large factor in the viability of SLB uptake, there is a strong case for Australian Right to Repair legislation which would encourage better product design that considers the product’s inevitable end of life disassembly. Using emissions standards and the Australian car market as an example, leaving this regulation to the US and EU does not guarantee Australia will receive better designed products.
Market Opportunity
We’ve shown nearly 60% of the discarded 18650 cells we collected could be reused. With a large volume of existing waste that is only growing there is no doubt of a plentiful supply of cells.
The specific market opportunity is beyond the scope of this project and the team’s capabilities however an excellent resource is the 100 page CSIRO document: Australian Landscape for Lithium Ion Battery Recycling and Reuse in 2020 – Current Status, Gap Analysis and Industry Perspectives.
A few key notes from the report which focuses on EVs:
- The global stockpile of EoL EV batteries is forecast to exceed 3.04 million packs by 2025 compared with 44,000 in 2018 and it’s estimated about 20 million EVs will be sold globally by 2025.
- An average EV battery has a life span of 8 to 12 years. Therefore, the share increase in sales of EVs since 2010 is providing a good source of second-life EV batteries as the first generation of retired EV batteries are starting to enter the market
- The market price for the SLBs ranged from 44 to 180 $/kWh based on Neubauer’s analysis
- The global EV battery reuse and recycling market generated $61.5 million in 2018 and is estimated to reach $7,809 million by 2025 with a CAGR of 99.8%
Ongoing Research
Rhino Instruments applied for and has been awarded a $25,000 Clean Economy Grant from the City of Greater Geelong for 2024/2025 that will allow us to continue developing the prototype BMS and take it through regulatory testing. If successful, the BMS would then be clear to be included as a component in a variation of the RM1 remote monitoring system, and be powered by an approved set of used 18650 Li-ion cells.
Beyond that, with further development the BMS could stand on its own in other applications. It should be noted though, that the BMS has been designed for low voltage, low current demand applications would need further modification or supporting electronics.