We disassembled 50 discarded lithium-ion battery (LIB) packs for our Sustainability Victoria supported grant investigating the commercial potential of reusing discarded lithium-ion cells. Discussing design might seem like a tangent, but when carefully placed hacksaws, other sharp implements, and brute force are the best ways to get into battery packs, you start to wonder if something has gone terribly wrong in product design.
Key Points
- Pack accessibility is directly related to the viability of circular principles
- Product design must incorporate end-of-life considerations if we’re to get serious about a circular economy
- There are encouraging signs of improvement in some newer packs
- Right to repair legislation will help drive these changes
- Australia should not rely on the US and EU to regulate, Australia needs its own right to repair legislation
Our Process
Important: This research is for informational purposes only and is not intended for personal use. Incorrect use or reuse of any battery, including lithium-ion, can cause fire, explosion, or death. Do not attempt to replicate this research or handle these materials at home. If you do choose to work with batteries, you do so at your own risk, and should ensure you throughly understand the inherent dangers and have the required electronics expertise.
Disassembling a lithium-ion battery pack is a tricky task. Each manufacturer builds their enclosure differently, with no manuals available. Some have screws holding them together, others hidden clips and glue. The cells inside are electrically connected to each other and live. Some packs have sustained damage that isn’t visible on the outside.
To undertake this process safely, we developed a solid procedure involving a risk assessment, safety protocols, PPE, accessible equipment for minor issues, and an emergency plan for worst-case scenarios.
With this plan in place, we were ready to go. As each pack was disassembled, we took note of the following:
- Assigned Pack ID
- Date Logged
- Manufacturer
- Pack Model Number
- Pack Voltage (New)
- Pack Amp hours (New)
- Number of Cells
- Cell Type/Size
- Physical Condition
- External Case Accessibility/Difficulty
- External Case Tools/Method
- Internal Enclosure Accessibility/Difficulty
- Internal enclosure Tools/Method
- Original Use
- Photo
- Any Notes
At the completion of our project we will release a case study that brings together everything we’ve published and also includes the disassembly data as a downloadable CSV file. UPDATE: Full case study and dataset available here.
Accessibility Ratings
The most interesting discovery in this process was rating the accessibility of the external and internal enclosures. Pack accessibility is directly related to the viability of the circular economy. If it’s too hard to dismantle a pack, it becomes unviable to recover the raw materials in their highest value form.
Originally, we had one rating but we quickly realised there are two enclosures: the one visible to the world and the one inside that holds the cells firm.
If we had to pick a favourite brand, it’s Ryobi. Somewhat sleek with some hidden screws but overall they seem to have the balance right. They consistently rated three (average difficulty) out of five for external and internal disassembly.
External case designs
In some cases, the difficulty of accessing the external case appeared to be about the sleekness of the design. The leading example of this is the Dyson cordless vacuum packs. The screwless design and the way the two plastic shells meet almost seamlessly make for a very nice-looking product that fits well in a home environment. Unfortunately that seamlessness also makes it impossible to open the case without destroying it.
At the other end of the spectrum, the Dewalt packs were super easy to open with eight simple Torx screws. The design of these battery packs is still pleasing, but they do look like they belong on the worksite and not in a kitchen.
Internal case designs
A high degree of difficulty was encountered once we were inside the packs. The cells need to be solidly held together so they can be electrically connected. Also, if you read the datasheet for any li-ion cell, you’ll note they are sensitive to impact and vibration. Therefore, product designers need to consider where the packs are likely to be used. Longevity, reliability, pack size, and the safety of the end user must be the balanced.
Dewalt and Milwaukee are two brands commonly seen on construction sites. These packs are likely the most abused on the market. Their packs were mostly rated ‘difficult’ to ‘very difficult’ to dismantle internally, but it seemed somewhat justified. On the other end of the scale, there are Dyson cordless vacuum packs which live in the home and are far less likely to experience regular impact and vibration. However, most of Dyson’s internal pack structures were almost as difficult to dismantle as construction-grade packs. In some examples, they were also more wasteful due to unremovable glue (likely part of thermal monitoring) stuck to several cells, preventing the recovery of those cells. There is an exception with Dyson, however. There appeared to be internal accessibility improvements in newer revisions of their packs, which deserves credit and is covered below.
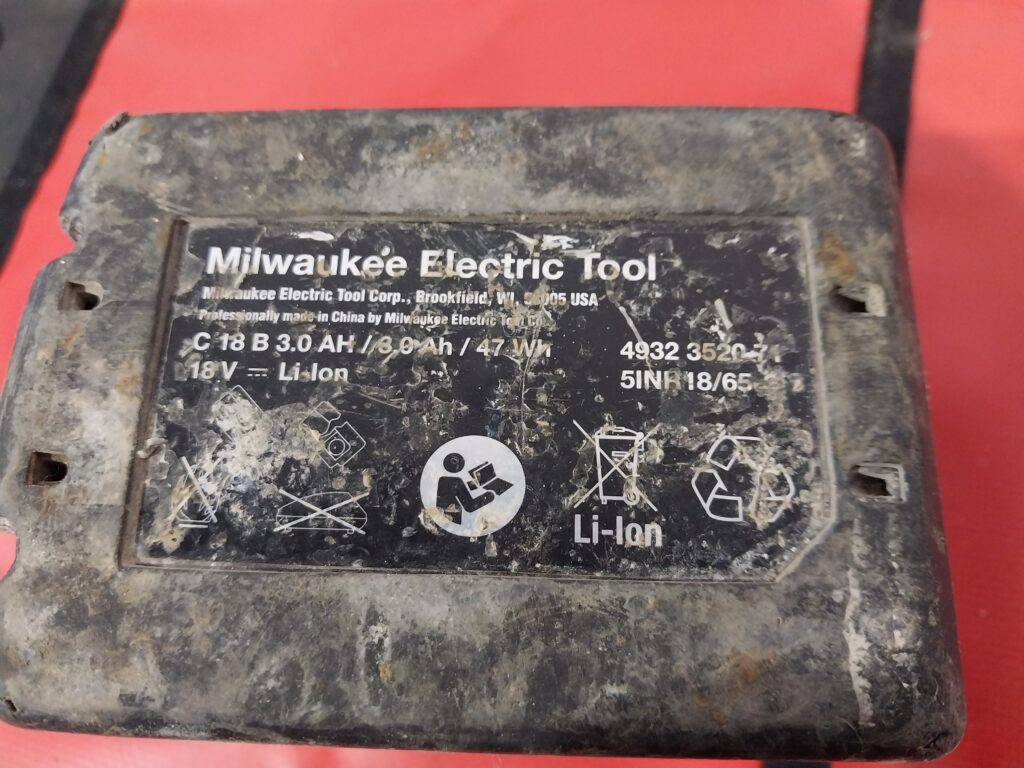
Maintaining Safety While Improving Design
Credit to Dyson here. A real bright spot in our dismantling journey was the discovery of invisible internal design improvements inside later model Dyson cordless vacuum battery packs.
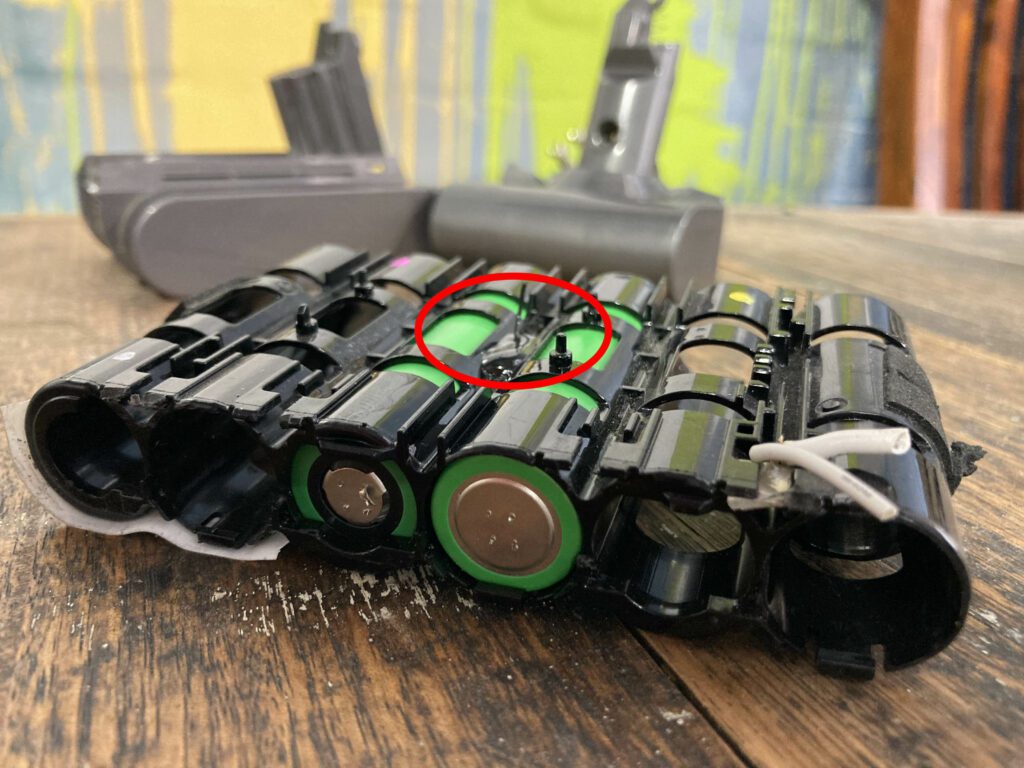
You can see the early packs have used glue inside. Our guess is that this is thermal glue that allows the temperature of two cells to be transferred to a sensor monitoring conditions. Cell temperature is an important metric in determining safe charging and operating conditions. If things get too hot, it’s important to slow charging or shut everything down to avoid fire or explosion. Quality packs that do this well and comply with regulations are the least likely to cause issues. Fires that you often see in the news are most likely non-compliant imported scooters and other products that haven’t passed stringent independent safety testing.
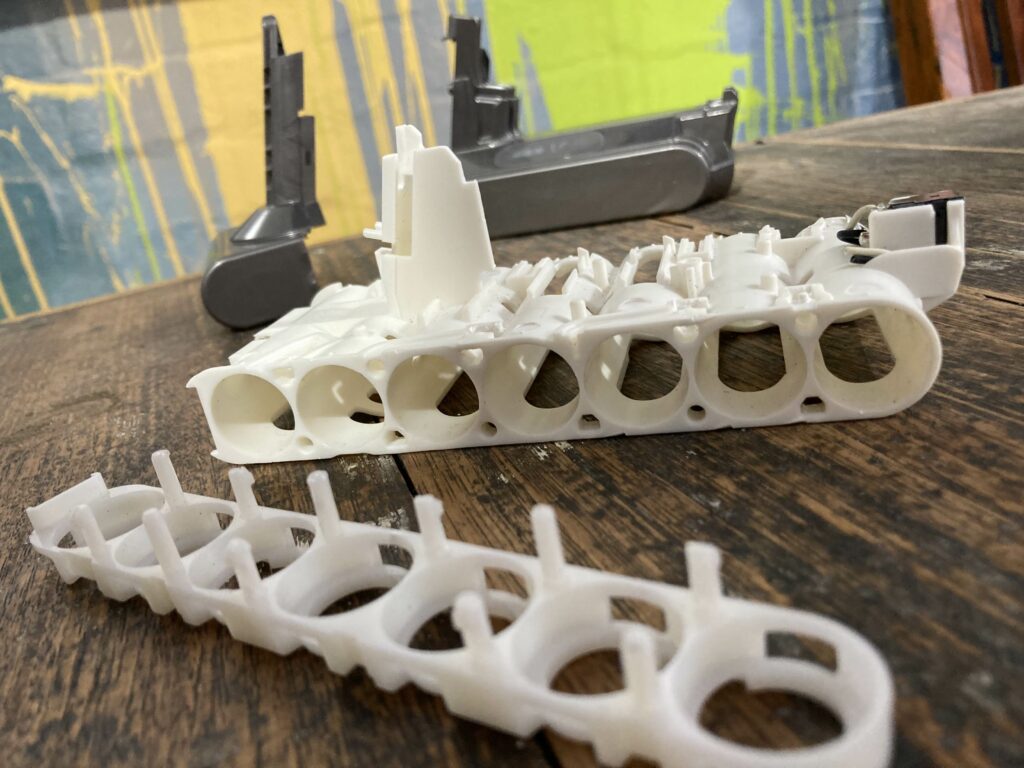
The later packs would have a similar ability to monitor cell conditions; however, these packs come apart with clips, and no cells are glued in, meaning all cells are fully extractable. Dyson appears to have achieved this without compromising the safety or reliability of their pack.
As we say, this was a pleasant surprise – once we were inside the pack. We’d still like to see screws on the outside of their packs to further improve end-of-life accessibility.
Right to Repair Has It Right
In the context of battery packs, there’s a real tension between accessibility and safety. If it’s too easy to get inside, a user may try to replace a single weak cell. That’s a plain bad and dangerous idea as the control circuitry is not designed for this change. We can see a product designer taking the approach that making an external pack so hard to open that you really need to destroy it is a safety feature. This ignores the inevitable fact that the pack will reach the end of its life and need to be dismantled though. It also misses that, as we’ve shown, there are still many (often most) viable cells inside ‘dead’ packs that could be reused paired with an innovative battery management system that ensures safety regulations are still being met.
The right to repair movement has been putting pressure on manufacturers to resist the temptation to lock everything down and prevent repairs. This has led to regulations that mandate products to be more accessible. Balancing an enclosure’s accessibility with durability, size, weight, safety, and manufacturability is hard but possible, so mandating it helps companies find the will to put in the extra effort.
For example, we don’t know the full extent of the reasons behind Dyson’s internal change to their later packs, but we suspect ensuring compliance with tightening regulations in the US and EU is a factor in their decision-making.
The Risk of Australia Becoming a New Electronics Dumping Ground
It’s important that Australia keeps up with the right to repair movement through regulation if it is to take the circular economy seriously. While it’s likely we will benefit from a growing right to repair movement overseas as companies try to keep their manufacturing lines simple by shipping the same product globally, there is the risk that we become a dumping ground for old clunker models.
In manufacturing, there is a high up-front cost to setting up manufacturing equipment and assembly lines. Over time, this cost gets paid off, and then the longer you can keep these old models in production, the higher the margins are, as the manufacturing equipment has been paid down. A parallel here is in the auto industry, which has been called out by the Climate Council of Australia for using Australia as a dumping ground for cars they can’t sell elsewhere. This is not a situation we want to repeat in other industries.